Hydraulic System Safety: How to Prevent Hose Failures and Pressure Accidents
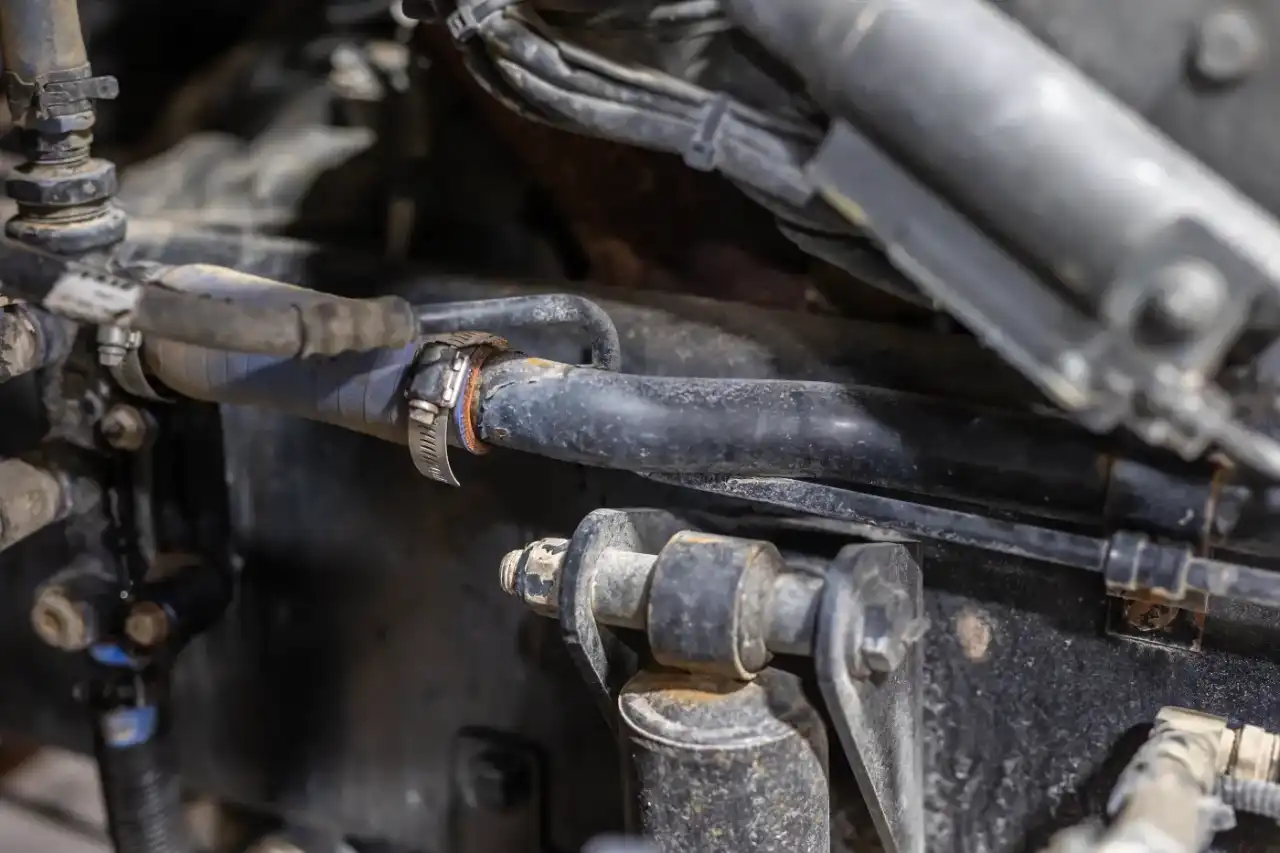
Introduction
Hydraulic systems are the powerhouse behind heavy-duty trucks, construction equipment, and industrial machinery, allowing for efficient movement, lifting, and control. These systems operate under high pressure, making them highly effective but also dangerous if components fail. One of the most common and hazardous failures in a hydraulic system is a ruptured or leaking hose, which can lead to fluid injection injuries, equipment breakdowns, and costly downtime.
Understanding how to prevent hydraulic hose failures and pressure-related accidents is crucial for maintaining safety, performance, and system longevity. This guide will cover the leading causes of hydraulic hose failures, safety measures to avoid high-pressure accidents, and best practices for maintenance.
How Hydraulic Systems Work and Why They Fail
A hydraulic system uses pressurized fluid to generate force and movement. This process relies on hydraulic pumps, hoses, valves, and cylinders to transfer power efficiently. When properly maintained, hydraulic systems are incredibly reliable, but when neglected, hose failures and pressure spikes can lead to serious hazards.
One of the biggest risks in a hydraulic system is a hose rupture. Hydraulic hoses are designed to withstand high pressure, but over time, they degrade due to wear, heat, and exposure to harsh operating conditions. When a hose bursts, fluid can escape at thousands of pounds per square inch (PSI), posing a direct safety risk to workers and causing immediate equipment failure.
Common Causes of Hydraulic Hose Failures
One of the most frequent reasons for hydraulic hose failure is excessive pressure. Hydraulic hoses are rated for a specific pressure range, and exceeding that limit can cause internal damage, leading to sudden bursts. Pressure surges, often caused by quick valve movements or blocked return lines, can create spikes that exceed the hose’s tolerance.
Another leading cause of failure is hose abrasion. Hoses that come into contact with sharp edges, rough surfaces, or other moving parts experience wear over time. Without proper routing and protection, the outer layer of the hose can degrade, exposing the internal reinforcement and making it more susceptible to leaks or ruptures.
High temperatures also accelerate hose degradation. Excessive heat causes hydraulic hoses to lose flexibility and become brittle, making them more prone to cracking. Overheated hydraulic fluid further worsens this issue by breaking down hose materials from the inside out, leading to internal damage that is difficult to detect until failure occurs.
Improper installation and incorrect fittings contribute significantly to hose failures. If a hydraulic hose is twisted, bent beyond its recommended radius, or secured with the wrong fittings, it places undue stress on the assembly. This stress weakens the hose over time, increasing the risk of failure. Additionally, incompatible hydraulic fluid can deteriorate the inner lining of hoses, causing soft spots, swelling, and leaks.
The Dangers of High-Pressure Hydraulic Failures
A hydraulic hose failure is not just an inconvenience—it is a serious safety hazard. When a high-pressure hose bursts, it can eject fluid at speeds capable of penetrating human skin. This type of injury, known as fluid injection, is often misdiagnosed as a simple cut, but the hydraulic fluid can cause severe tissue damage, infection, and even amputation if not treated immediately.
Uncontrolled hydraulic fluid leaks can also lead to slip hazards, fire risks, and environmental contamination. Many hydraulic fluids are flammable, and a leak near an ignition source can cause a fire. Additionally, hydraulic leaks contribute to soil and water pollution, making proper maintenance essential for both safety and environmental responsibility.
A pressure-related accident can damage critical components, causing complete equipment failure. When a hydraulic cylinder or pump is exposed to sudden pressure spikes, seals can rupture, leading to loss of hydraulic control. If this occurs in lifting or braking systems, it can result in catastrophic failure, putting both operators and bystanders in danger.
How to Prevent Hydraulic Hose Failures
Routine hydraulic hose inspections are essential for detecting early signs of wear and preventing failures. Operators should check for cracks, bulges, leaks, or abrasions along the hose surface before and after each use. Any stiff or discolored hoses should be replaced immediately, as these are signs of internal damage.
Proper hose routing and installation reduces stress on hydraulic lines. Hoses should be routed in a way that prevents excessive bending, twisting, or direct contact with sharp surfaces. Using protective sheathing and clamps helps minimize abrasion and vibration-related wear. Selecting the correct hose length and fittings ensures that the system operates within its designed pressure range.
Using hydraulic fluid compatible with the system’s hoses and seals prevents internal degradation. Many hydraulic fluids contain additives that can either protect or deteriorate hoses, depending on their chemical composition. Always use manufacturer-approved fluids and avoid mixing different hydraulic oils unless compatibility is confirmed.
Installing pressure relief valves and surge suppressors helps protect hydraulic hoses from pressure spikes. These components regulate flow fluctuations and prevent sudden pressure increases that can lead to hose bursts. Regularly testing and calibrating pressure control devices ensures that they are functioning correctly.
Maintaining proper fluid temperature helps extend hose life and reduce system strain. Overheating is often caused by clogged filters, low fluid levels, or excessive load demands. Keeping cooling systems and fluid reservoirs clean prevents heat buildup and ensures that hydraulic components function at optimal efficiency.
Best Practices for Hydraulic Safety
Every operator working with hydraulic systems should wear personal protective equipment (PPE), including gloves, safety glasses, and protective clothing. This provides a barrier against unexpected fluid leaks or high-pressure spray.
Before performing any maintenance on hydraulic systems, operators should always release system pressure. Many hydraulic failures occur when a technician removes a hose without first depressurizing the system. Even after shutting off the equipment, residual pressure can remain trapped in hydraulic lines, which must be safely released before disconnecting any components.
Operators should never use their hands or fingers to check for hydraulic leaks. Even a small pinhole leak can inject fluid into the skin, causing severe internal injuries. Instead, a piece of cardboard or wood should be used to safely detect leaks without risking exposure to high-pressure spray.
Using factory-recommended replacement parts ensures that hydraulic components remain compatible and function correctly. Many breakdowns occur when aftermarket or mismatched hoses and fittings are used, leading to leaks and improper pressure regulation. Following manufacturer guidelines for hose ratings, pressure limits, and fluid compatibility helps prevent failures and accidents.
Regular hydraulic system training for operators and maintenance personnel ensures that safety protocols are followed correctly. Many hydraulic accidents occur due to lack of knowledge or improper procedures, so training programs should cover hose handling, pressure release methods, and emergency response.
When to Seek Professional Hydraulic Repairs
If a hydraulic system is experiencing frequent hose leaks, sudden pressure drops, or excessive heat buildup, it’s time to seek professional servicing. Persistent issues may indicate a deeper system failure, such as worn-out seals, failing pumps, or incorrect pressure regulation.
If a hose bursts unexpectedly, replacing it without diagnosing the root cause of failure could lead to repeated breakdowns and safety risks. A hydraulic specialist can inspect the entire system, check for hidden issues like internal blockages or worn-out fittings, and ensure that replacements are properly rated for the system’s pressure requirements.
For expert hydraulic system repairs, hose replacements, and pressure diagnostics in Jackson, NJ, contact A&G Equipment and Truck Repair today.
Contact us
At A&G Equipment and Truck Repair, we prioritize the smooth operation of your heavy equipment, farm equipment, and trucks. For more information on our hourly mobile rate or to schedule an appointment, please contact us today!